超短パルスレーザー(ピコ秒レーザー・フェムト秒レーザー)とは?
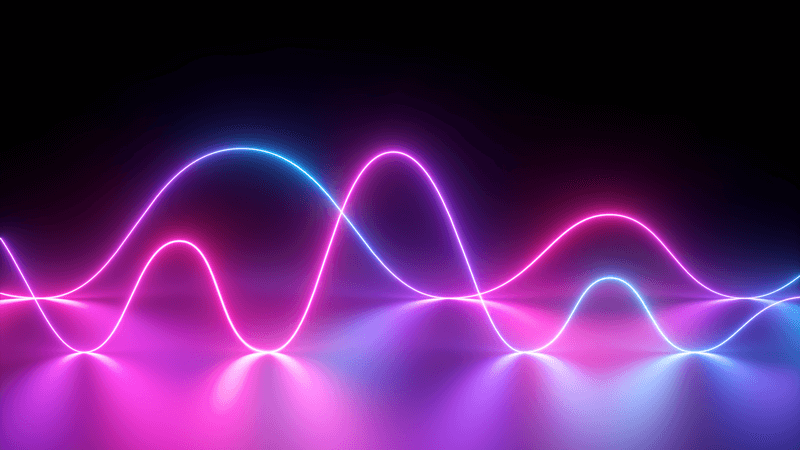
パルス幅が数フェムト秒から数ピコ秒のレーザーを、超短パルスレーザーと呼びます。場合によってはピコ秒レーザー、もしくはフェムト秒レーザーと呼ぶケースもあります。
レーザーの発振動作は、連続波発振動作およびパルス発振動作の二つに分かれており、一定の出力を連続発振するものを、「連続波発振動作」と呼びます。
一方「パルス発振動作」は、パルス状の出力を一定の繰り返し周波数にて発振します。超短パルスレーザーは、パルス発振動作の中でも特にパルス幅が短いレーザーです。
超短パルスレーザーは、広い発振幅を有する特性があります。例えば、「チタンサファイアレーザー」は広く普及している超短パルスレーザーのひとつですが、660から1180nmと非常に幅広いスペクトルで発振できます。
超短パルスレーザー(ピコ秒レーザー・フェムト秒レーザー)のメリット
続いて、超短パルスレーザーのメリットについて解説しましょう。
高精度な微細加工が施せる
大きなメリットのひとつが、熱の影響が少ないため高精度な微細加工ができることです。短時間で高いピーク出力を作用させることによって、表面を分解・蒸散します。
光のエネルギーが吸収されて熱に変わる時間はおよそ10ピコ秒だといわれています。
超短パルスレーザーが持っているパルス幅はそれよりも短時間なので、熱による影響が少なく、やけやクラック、バリも減少、その結果高品位な仕上がりが可能になります。
衝撃や負荷が軽減できる
超短パルスレーザーは非接触加工なので、材料に直接触れることはありません。そのため、材料に衝撃や負荷などの影響が起きるのを少なくできる、というメリットもあります。
従来なら加工が難しいとされてきた複合素材などの材料への加工も可能。従来のレーザー加工における課題を解決できる工法として注目を集めています。
微細加工に対応可能
超短パルスレーザーは、加工部の周辺にバリが発生しないので、高精度かつ高品位な微細加工が叶います
またトリミングやマイクロテクスチャー、穴あけなどの微細形状にも対応できるので、幅広い要望に応えられるでしょう。
超短パルスレーザー(ピコ秒レーザー・フェムト秒レーザー)のデメリット
さまざまな材料へ加工できる超短パルスレーザーですが、いくつかの注意点もあります。それぞれ詳しく解説しましょう。
ガラス同士の接合に課題がある
超短パルスレーザーを用いてガラス同士を接合させる際の課題が、加工効率の低さ。ガラスを溶融する場合、ひとつの接合点に対し数百パルスにおよぶ繰り返し照射が必要です。
しかし、繰り返し周波数はパルスエネルギーと両立できません。そのため、いくら照射しても時間平均出力は数ワット程度。これでは決して効率が良いとは言えないでしょう。
また、溶融領域が小さいので、隙間に溶けたガラスを充填するためには隙間の厚さをごく薄くしなければならない、という課題も残っています。
コストが高く量産性が低い
コストが高い超短パルスレーザーは、大量生産には向きません。また条件出しに時間がかかるため、最適加工数はせいぜい1から1000個程度でしょう。ただし、専用機があれば数万個の加工にも対応できます。
超短パルスレーザー(ピコ秒レーザー・フェムト秒レーザー)の用途
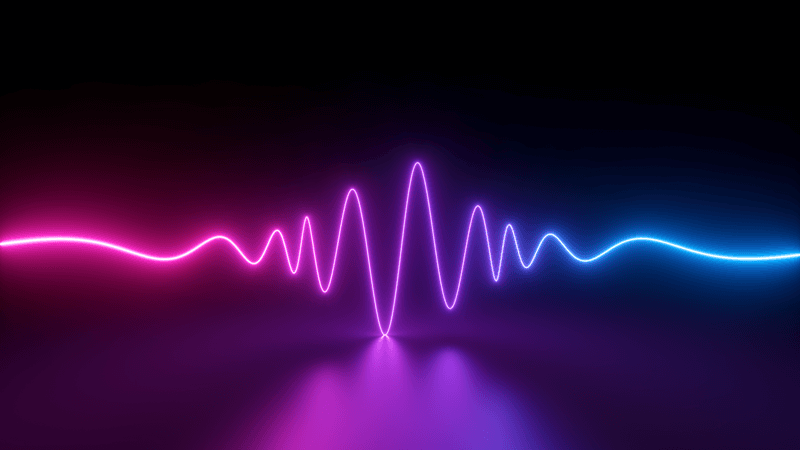
ここからは超短パルスレーザーの用途を具体例とともに紹介しましょう。
微細加工
超短パルスレーザーがその能力を発揮するのは微細加工です。現代では技術の発達により、製品の小型化が進んでいます。
例えば電子機器などの場合、商品が小型化すれば当然基盤も小型化。中でも半導体の製造では、シリコン材やガラス版の上に「薄膜材」が使用されています。
この薄膜の加工こそが、微細加工のひとつです。ナノ秒レーザーのおよそ1/10も細い超ピンポイント加工ができるので、薄膜材などの繊細さと正確さを求められる加工に適しています。
医療・美容
超短パルスレーザーは、生体組織を精密かつ無損傷で蒸散できる作用を持っています。そのため美容や医療の分野においても活躍中。
従来の美容レーザーよりも短いパルス幅で照射できるので、熱による肌の負担が少ないままでメラニン波を粉砕できます。
また、レーザーが肌の奥深くに届くので、ニキビ跡やシミ、そばかすなどを解消する効果が期待できるでしょう。
その他
従来のレーザーでは加工が難しかった材料の加工も可能です。たとえば窒化ガリウム・炭化シリコンなどのワイドバンドギャップ材料は、加工に大きなエネルギーが必要です。
そのため、これまではレーザーによる加工は難しいとされていました。
しかし、高い出力を持つ超短パルスレーザーなら、ワイドバンドギャップ材料も加工可能。そのほか、セラミックやシリコン、ガラスといった脆性材料に対しても、高品位な加工が施せます。
超短パルスレーザー(ピコ秒レーザー・フェムト秒レーザー)についてのまとめ
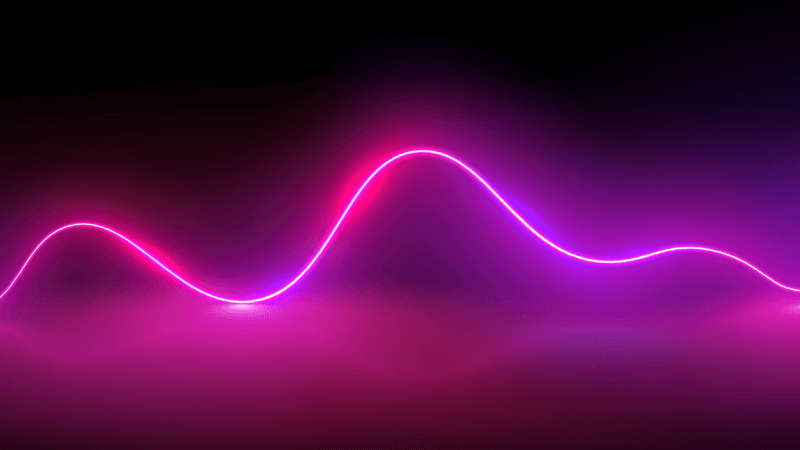
超短パルスレーザーは、非接触・非加熱・高出力という性質を活かし、さまざまな用途に活用されています。しかし、使用するにあたって、効率性や生産性で課題が残っているのも事実です。
業務に導入する際は、特性やメリット・デメリットをしっかり理解したうえで、事業にどのように活かせるかを考えることが大切です。